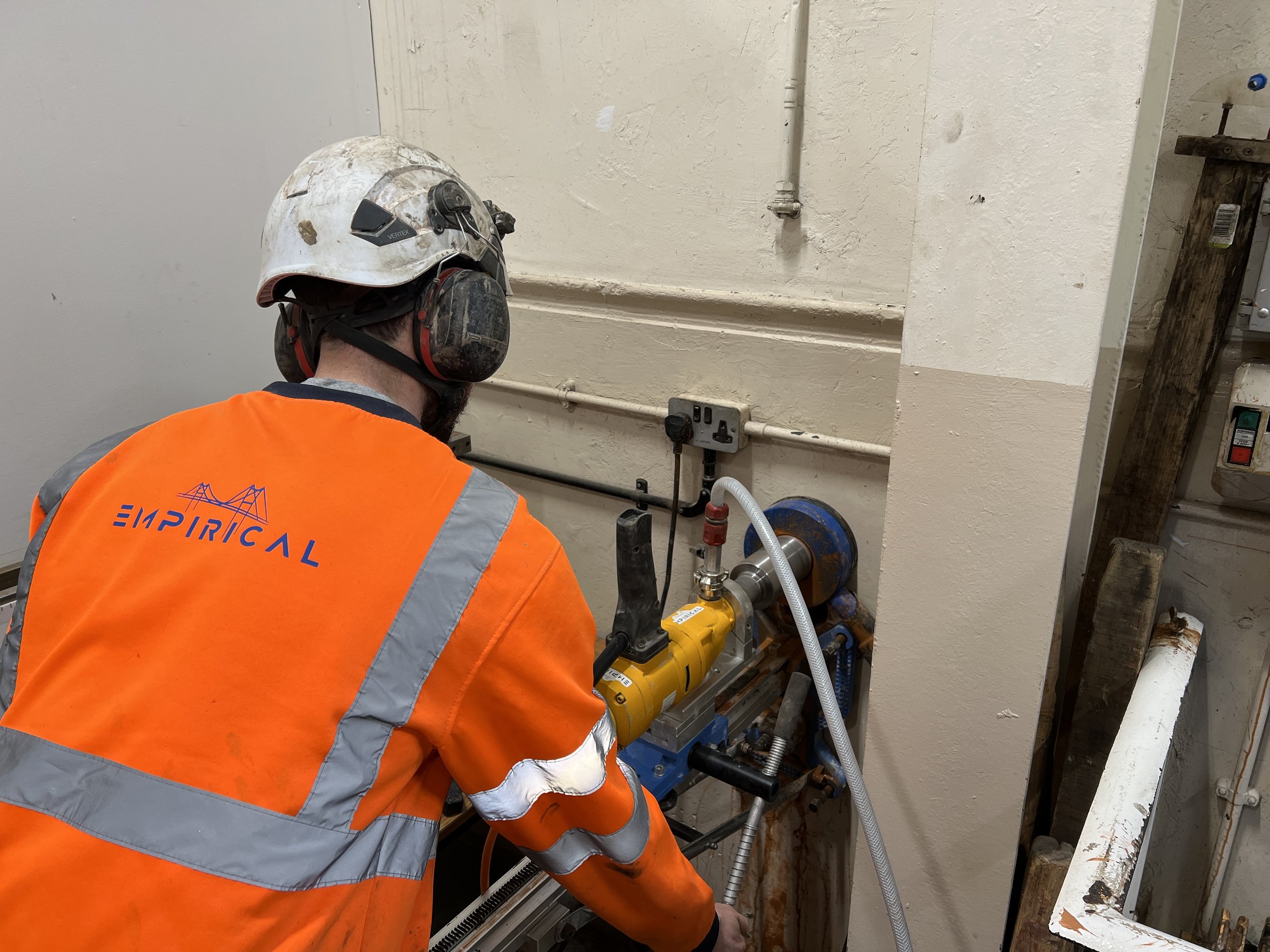
MATERIALS SAMPLING AND TESTING
Empirical’s expertise in the sampling and testing of various materials ensures the required material properties can be ascertained accurately and with confidence. This includes the sampling of structural materials or non-structural materials to assist potential design or assessments of a particular element. Our clients can be confident that the testing is being conducted to the correct standards with our approved UKAS accredited laboratories. A summary of our typical material sampling and testing services are detailed below, however the below is not fully exhaustive. Should you have a particular requirement please contact us and we can be certain to help with our industry knowledge and our approved partners. With Empirical expertise our clients can be assured samples are recovered as per the requirements, accurately and with minimal disruption. Empirical ensure the sample & test locations are reinstated using suitable repair products to meet client’s requirements in accordance with manufacturer’s instructions & repair guidelines.
Concrete Testing – Ascertain mechanical properties, mix constituents and level/degree of contamination or possible cause of defects.
Visual Examination – A simple method to determining quality of concrete which can provide a speedy assessment of the concrete quality. A simple visual examination can quickly assess the degree of compaction, excess voidage, aggregate type/size and distribution as well as potential presence of any cracking or further degradation. A visual examination undertaken by Empirical experienced engineers enables a quick visual assessment of the concrete for clients and enables a more targeted and detailed laboratory testing regime. This would typically involve the extraction of concrete core specimens for in house visual examination.
Concrete Compressive Strength Testing – The extraction of concrete cores in accordance with BS EN 12504: 2019. Empirical experienced operatives ensure the cores are extracted in accordance with the standards with minimal damage to the structure. Prior to any coring, a GPR or cover meter survey is conducted to ensure no embedded elements are cut during the coring process. Another important standard which should be considered for the assessment of compressive strength in structures and precast concrete components is BS EN 13791: 2019. Following sampling the cores are received by our UKAS approved laboratory where they are examined for degree of compaction, cracks, voids and honeycombing. Concrete cores are the most accurate and reliable method of ascertaining the in-situ concrete compressive strength.
Concrete Petrographic Analysis – Petrographic analysis can be undertaken on concrete samples (typically core specimens). Petrographic analysis is used to provide detailed properties of the hardened concrete. Our approved UKAS accredited laboratory undertakes the petrography in accordance with BS 1881-211, ASTM C856 and APG-SR2. Our standard petrographic testing report would typically include information on the aggregate type/grading, the presence of expansive or shrinkable aggregates, cement type, presence of cement replacements, presence of any deleterious elements such as chemical/chloride/sulphates, fire damage assessment, presence and cause of microcracking/cracking, alkali aggregate reaction (AAR) or Alkali Silica Reaction (ASR), delayed ettringite formation and water/cement ratio.
Cement Content Testing – Cement content of concrete is an important aspect to understand the durability and strength of concrete specimens. Cement contents can be determined by means of extracting concrete powder drillings, concrete lumps or concrete cores. Our approved UKAS accredited laboratory undertakes the cement content analysis in accordance with BS 1881:Part 124:2015+A1:2021. The cement content of concrete specimens can also be determined via petrographic analysis as detailed above.
Chloride Content Testing – Chloride content of concrete is essential for understanding the risk of corrosion due to either chloride ingress from external sources or from cast in chlorides. Calcium chloride was commonly used as an accelerating admixture in concrete up until the mid-1970s for pre-cast concrete elements. The code of practice was amended which effectively banned the use of calcium chloride, however concrete products/structures built prior to this have a potential to contain ‘cast in’ chloride, resulting in a risk of corrosion to the embedded reinforcement. Furthermore, the exposure of particular elements may expose them to high levels of chloride such as marine structures or highways structures due to the use of de-icing salts. Empirical ensure that a suitable sampling procedure is adopted to enable the risk of chloride induced corrosion occurring to a particular element. Chloride contents can be determined by means of typically extracting incremental concrete powder drillings, concrete lumps or concrete cores. Our approved UKAS accredited laboratory undertakes the chloride content analysis in accordance with BS 1881:Part 124:2015+A1:2021.
Sulphate Content Testing – Sulphate content testing can be essential to ascertain the potential cause of visible degradation. Sulphate can be present in concrete from either an external source for example buried elements from the soil or from an internal source of contaminated aggregates. Sulphates cause an expansive reaction which breaks down the matrix affecting the concrete quality and durability. Sulphate contents can be determined by means of typically extracting concrete powder drillings, concrete lumps or concrete cores. Our approved UKAS accredited laboratory undertakes the sulphate content analysis in accordance with BS 1881:Part 124:2015+A1:2021.
Alkali Content Testing – Understanding the alkali content of concrete can be a further way of ascertaining the potential cause of visible degradation. This is due to deleterious reactions involving the aggregate and the surrounding cement paste. This is commonly in the form of a reaction between reactive alkalis contained in specific types of aggregate and alkalis within the concrete derived from the cement. Sulphate contents can be determined by means of typically extracting concrete powder drillings, concrete lumps or concrete cores. Our approved UKAS accredited laboratory undertakes the alkali content analysis in accordance with relevant standards and codes of practice.
High Alumina Cement Content (HAC) – High Alumina Cement (HAC) has been historically used mostly in pre-cast concrete products. HAC was used during the casting of structural elements due to its rapid hardening properties enabling pre-cast products to be used in service earlier than Ordinary Portland Cement (OPC) products. However, several problems occurred with structural elements in the 1970s, in some instances resulting in the premature failure of structural elements and this in turn resulted in the ban of the use of HAC in the mid-1970s. HAC is known to undergo a phenonium commonly referred to as conversion which results in a reduction in compressive strength. Although; to this date there is still a large number of structures which have HAC structural elements requiring careful identification, testing and monitoring. HAC structures may remain serviceable as long as certain conditions are met ensuring the elements are not exposed to high levels of humidity, moisture and temperature. HAC content can be determined by means of typically extracting concrete powder drillings, concrete lumps or concrete cores. Our approved UKAS accredited laboratory undertakes the a rapid chemical test in accordance with BRE Information Sheet IS 15/74. Furthermore, there may be a requirement to understand if the concrete has undergone conversion and ascertain the degree of conversion.
Carbonation – Standard good quality concrete creates an alkaline environment which affords protection to the embedded steel reinforcement. This is due to the concrete alkalinity producing a passive oxide layer on the reinforcement protecting it from corrosion. Concretes alkalinity can be neutralised by the atmospheric gases causing the protective passive layer to be broken down resulting in corrosion of the embedded reinforcement this process is commonly referred to as Carbonation induced corrosion. Concrete carbonation is a function of the concrete quality and the rate at which this occurs is dependant on the quality. Therefore, it is essential to understand the depth of concrete carbonation alongside the depth of concrete cover (see cover meter) to the embedded reinforcement. Concrete carbonation can be measured in-situ on freshly broken concrete surface using phenolphthalein indicator solution or in the laboratory following extraction of concrete core samples the tests undertaken in general with guidance given in BRE Information Sheet IP6/81 & BS EN 14630:2006.
Mortar Testing – Mortar is a commonly used building material found on most structures, whether modern or historical. These mortars have changed over time although the materials primary function remains the same. This is even more so apparent with modern day mortar where cement replacements and supplementary cementitious materials are used to reduce the environmental impact and increase performance. Therefore, there is a need to understand mortar properties for the purpose of establishing compliance with a specification, as part of a failure investigation or as part of structural assessment.
Mix proportion Analysis – Mortar mix proportion analysis is a common method used to understand the mortar constituent material contents and ascertain the traditional mix designation or modern mortar classification. Mortar mix proportion analysis is typically undertaken on lump samples extracted from the mortar beds in accordance with the codes of practice and can be determined by means of chemical analysis in accordance with the methods described in BS 4551.
Timber Inspection / Testing – It is essential to undertake on site in-situ visual examination and moisture readings to timber elements to enable accurate condition assessment of timber elements. Empirical adopt an on-site and laboratory testing approach on discrete samples to enable a detailed understanding of the condition. Empirical approved timber specialists give our clients a high level of certainty in timber condition assessments.
Sulphate Content – Sulphates can have a detrimental effect on mortar performance and can result in the degradation of mortar. Therefore, as part of a mortar failure investigation it is essential to understand the sulphate contents with a view to confirming the possible cause of the degradation.
Natural Masonry Testing – Masonry is a commonly used building material for historic bridges and buildings. To enable assessment of the structures, there is a requirement in some instances to ascertain its strength. Given masonry structures are constructed from a natural material the strength can vary significantly therefore it is essential to understand the strength accurately. Empirical offer this by means of extracting core samples as per the sampling requirements ensuring cores are of sufficient length & diameter. Masonry compressive strength of cored specimens can be ascertained in accordance with the methods described in ASTM D7012.
Species Type – Ascertain species type to enable assessment of specific species properties.
- Moisture Content – In-situ moisture readings undertaken alongside samples for gravimetric moisture content to assess the level/risk of degradation.
- Decay – Ascertain the extent and type of visible decay for the purpose of assessment and scheduling repairs.
Brick / Masonry Unit Testing – Understanding the strength of brick or masonry units where the properties are unknown, or alternatively where they are degrading requiring an assessment of the possible cause.
- Water Absorption Testing
- Sulphate testing
- Compressive Strength to BS EN 772-1
Paint (Protective Coating) Testing –
- Toxic Metal in Paint – There was significant lack of regulation with regards to the addition of toxic metals such a lead to paints historically. Prior to any refurbishment or removal of paint it is necessary to assess the risk and understand the presence and levels of toxic metals within protective coatings.
- Polymer Type – Part of refurbishment or heritage projects it may be essential to understand the exact polymer type to enable suitable overcoating or specification of the new protection system.
- Paint Compatibility – A compatibility report will recommend suitable overcoating or protection systems that comply with the existing system or recommend suitable preparation methods to achieve a durable protective coat.
Metallic Testing
- Metal Type Identification – Visual & chemical analysis to understand the material type.
- Laboratory Hardness Vickers Testing (Hv) - The undertaking laboratory hardness tests on metal nick sample cross sections using the Hardness Vickers in accordance with the method described in BS EN ISO 6507-1 2018. Allowing the approximate tensile strength to be estimated using tables in BS EN ISO 18265:2013.
- Tensile Strength Testing - The undertaking physical tensile tests on metal coupon or reinforcement samples in accordance with the method described BS EN ISO 6892-1 : 2019 B20.
- Cast Iron Strength Assessment – Ascertain the strength properties of cast elements by means of extraction of discrete core samples for subsequent laboratory tests.
- Spark Analysis (Carbon Equivalent / Weldability) – Ascertain carbon equivalent value to enable suitable welding techniques and repairs to be specified.